In this blog post, we will provide 12 real-world examples of how to cut the cost of materials for home construction. By implementing these steps, it’s possible to save money on materials without sacrificing quality. This guide aims to provide a step-by-step process to help you save money when buying building materials.
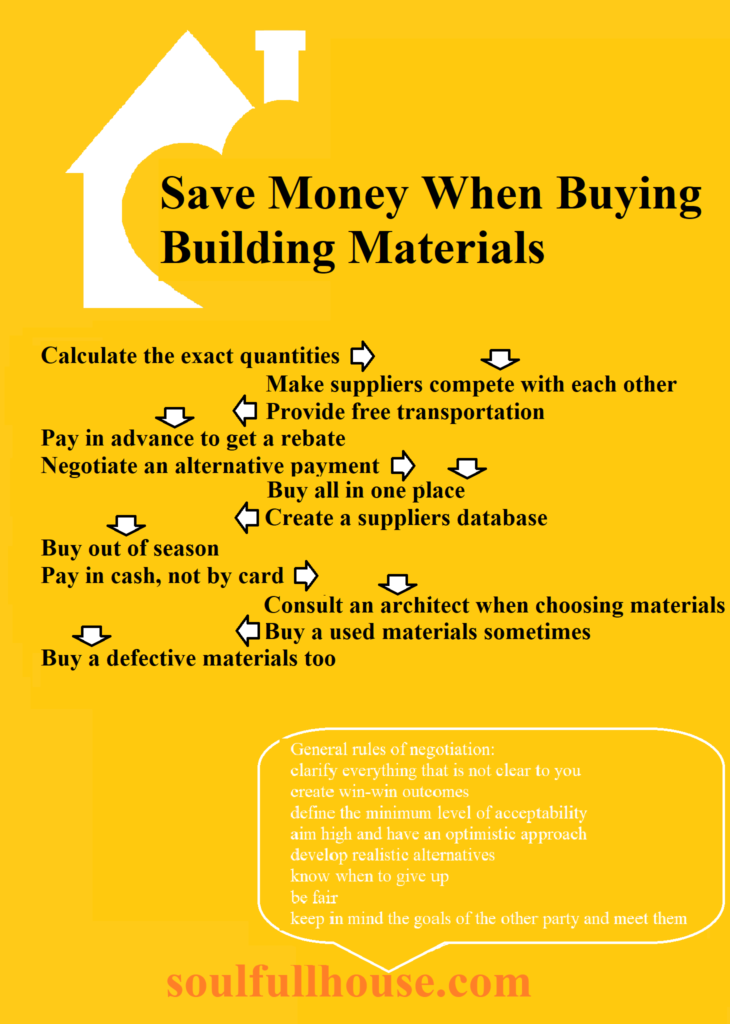
These are 12 real-world examples of how you might cut the cost of purchasing materials for your home’s construction in half:
- Calculate the exact quantities
- Make suppliers compete with each other
- Provide free transportation
- Pay in advance to get a rebate
- Negotiate an alternative payment
- Buy all in one place
- Create a suppliers database
- Buy out of season
- Pay in cash, not by card
- Consult an architect when choosing materials
- Buy a used materials sometimes
- Buy a defective materials too
Making a clear savings plan and sticking to it is the greatest method to save money when building a house. The best time to put together such a plan is when you’re designing a house, and the best time to start working on saving is straight after! This is critical to remember because if you do not address this issue quickly, you will be unable to implement many of the options that we will give to you.
The objective we must set for ourselves is to save as much money as possible by spending our own effort and time while not sacrificing quality.
Although arranging the building of a house with one contractor and requiring him to handle material procurement is more simpler and easier, it is also far more expensive. Separating material procurement processes and contractor interaction is the first step in creating a savings plan. Then continually follow the guide we’ve provided below!
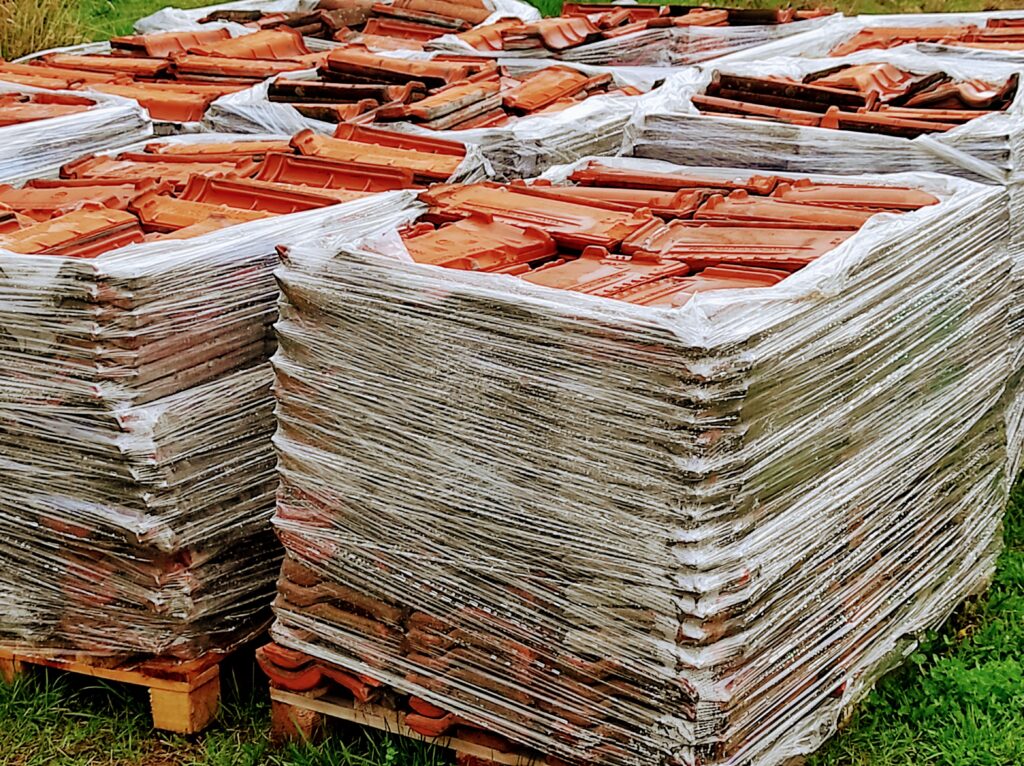
The ultimate, step-by-step, guide to saving when buying building materials!
We must state certain critical points right from the start. First and foremost, this guide assumes the employment of general negotiating strategies, which we will list in an appendix at the end of the text. Second, this is not about deploying tricks or gimmicks (much alone scams), but rather consistently used arrangements that benefit all stakeholders, the consumer and the supplier. Yes, the seller makes a profit by offering you a discount or some other benefit; otherwise, there would be no contract.
12 ways to save when buying building materials!
The steps that follow are not listed in order of priority, or any other order, and do not exclude each other! So, you can be creative and combine them for one and the same item.
1. Calculate the exact quantities
After construction is completed, each construction site is littered with various materials. All of the material has been paid for, and it is a total loss. Of course, it is impossible to purchase the exact amount required, but keep in mind that contractors calculate 20 to 30 percent more material than is required, especially for basic works, because the only thing that matters to them is to complete the work as soon as possible, and any delay caused by the delivery of an additional amount of material is a complete waste of money. As a result, it is far wiser to submit the production of the materials specification for building a house to an architect or designer, and to demand that it be as precise and complete as possible. All of the minor details that frequently slide through the cracks during the calculation can have a substantial negative impact on the price, but if we compute them in time, they can also become part of the discount arrangement.
2. Make suppliers compete with each other
Of course, one of the first steps in any transaction is to visit merchants and compare prices. But, because we will be spending a lot of money on materials when building a house, we should not stop here. After you’ve determined where you can get the best bargain by conducting an initial search (it’s easier to do this online), go to a few more merchants and provide them with the best deal you’ve found. Then request a better offer from them! It is obvious that you will then take that new, more advantageous offer to the first merchant and repeat the procedure until you have squeezed out every last dollar of the discount.
Believe me, as someone with many years of experience building houses, there is no more effective technique to cut material costs!
3. Provide free transportation
If paid in full, the cost of transporting supplies to the construction site can greatly raise the total cost of material acquisition. There are two approaches to virtually totally reduce these costs. The first is self-evident: request that the supplier provide free transportation as a type of discount. But there is another alternative if the provider is unable to provide free transportation or has already provided you with some other form of discount. We usually buy from retailers and not from the manufacturer itself, so they also need to transport materials to their location. In that case, you ask the hauler, who delivers the goods to the retailer, to stop by your construction site first, and unload the material you bought and then to move on.
4. Pay in advance to get a rebate
Offer an advance payment in the amount of the complete purchase to the supplier from whom you chose to buy at the outset of the design process, i.e. months before the start of building.
Liquidity is one of the most fundamental difficulties that any organization encounters. To have enough cash on a daily basis, even very profitable enterprises that are solvent must sometimes take out expensive loans. This is your chance to get a spectacular deal! According to my experience, many suppliers in this situation will give material for nearly the same price as their purchase price. Even if you don’t have a margin on your goods, it pays them to sell to you because the sale is effectively an interest-free liquidity loan for them.
5. Negotiate an alternative payment
It should never be forgotten that suppliers require a wide range of services and items as well. Perhaps you can supply some of that, or you know someone (friend, relative, neighbor, etc.) who can do it and owes you a favor…??? In any case, it is worthwhile to try to negotiate such a non-monetary arrangement in order to save some much-needed money.
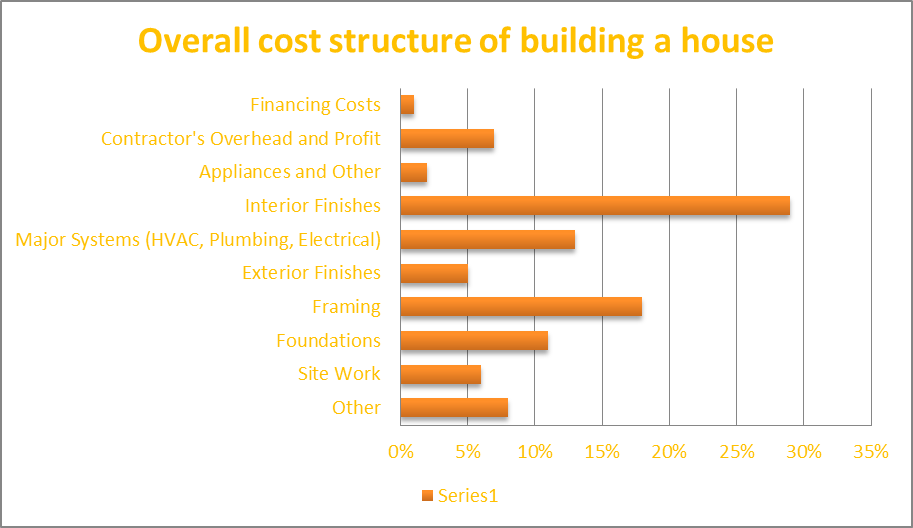
6. Buy all in one place
The universal rule is: the larger the cost, the greater the discount! As a result, make sure to correlate the purchase of smaller amounts in your specification with the purchase of bigger amounts. Also, if you know someone who is doing construction work at the same time as you and requires the material, offer to share the cost.
7. Create a suppliers database
Nowadays, there is no doubt that IT accelerates, facilitates, and increases the success of any organization. It is not essential to purchase pricey software; simply create a high-quality, comprehensive table in EXCEL. Inside, you’ll enter information about who in your neighborhood offers what, at what starting pricing, how many discounts it offers, whether it’s ready for other concessions, and so on… Each individual provider should also provide references. Create this database as soon as feasible and fill it out completely!
8. Buy out of season
Construction is a seasonal activity, and so is material buying. At the start of winter, the pace of activity slows, material sales diminish, and the final financial reports are prepared. As a result, discounts are plentiful this time of year and should be taken advantage of! Don’t be concerned about a lack of storage space on your job site; it’s often possible to store the stuff at the dealer until you need it.
9. Pay in cash, not by card
As with any other purchase, when you enter into price reduction negotiations with cash in hand, the probability that an agreement will be reached increases drastically.
10. Consult an architect when choosing materials
We’ve already mentioned that you’ll need an architect to create a material specification. However, there is another critical activity for which you require his assistance: material acquisition – selecting the best! Not the best, but the best!!!
Modern architecture features a wide range of materials that can all be employed for the same function. Their constructive characteristics are typically fairly similar, with the distinction occurring in aesthetics. A professional architect is aware with the complete market offer and can recommend an alternate material that is more economical while still acceptable to you aesthetically.
One more important note! When choosing a material, in addition to its purchase price, it is important to immediately calculate the price of the work. Different materials require different installation techniques, and they cost differently. It can happen that cheaper material requires more expensive work, so there is no saving in the end.
11. Buy a used materials sometimes
This may appear to be a desperate move, but it is not. Please bear with me! The material has only a beneficial role in some works. Just because it has been used and does not look perfect does not indicate it will perform poorly. You will save money and the environment will benefit. In some circumstances, the material utilized contributes to the home’s beauty and warmth. Consider brick, wooden beams, or a floor…
12. Buy a defective materials too
When discussing the purchase of damaged material, it is critical that it be both constructively and aesthetically correct. In this scenario, the reverse logic from the first step is correct. You should buy more than you need, set aside and discard unsuitable items, and the savings are achieved on a significant price difference compared to the usual.
BONUS: General rules of negotiation
- clarify everything that is not clear to you
- create win-win outcomes
- define the minimum level of acceptability
- aim high and have an optimistic approach
- develop realistic alternatives
- know when to give up
- be fair
- keep in mind the goals of the other party and meet them
In conclusion, there are many ways to save money on building materials when constructing a home, and the 12 techniques listed in this post are just the beginning. It is important to remember that each strategy may not work in every situation, but by combining and being creative with these methods, homeowners can potentially save a significant amount of money on their home construction projects without sacrificing quality. By creating a savings plan and putting in the effort to negotiate and find the best deals, homeowners can make their dream homes a reality while keeping costs down. Remember to always approach negotiations with respect and fairness to ensure a win-win situation for both the consumer and the supplier.